How is powder coating of metal products carried out?
Today, many have heard about polymer coatings, but not many know how the application process occurs, especially when you consider that these are not liquid paints familiar to everyone, but a powder that is sprayed onto the metal under the influence of electricity. In this article we will talk about what powder coating of metal products is and how it happens in large industries and in small private workshops.
The content of the article
Polymer powder
The composition of polymer powder is a complex chemical formula, which makes no sense to dwell in this article. Simply put, it is a heat-resistant, electrically charged powder for painting metal, which does not require dissolution in active solvents.
Today, this dye is increasingly used for painting cars and their individual parts, which are most exposed to negative effects.
Interesting! Painting metal with powder paint is not a cheap pleasure, and after carrying out all the work, the price of a product can go up several times.
Theoretically, powder coating of metal can be carried out in a garage or a mini-workshop, but you can’t do without buying specialized equipment.
As we said above, the painting takes place under the influence of electricity, that is, the spray gun must not only blow the powder through the nozzle, which in itself is an impossible task for simple tools, but also charge the paint with a positive charge of energy. Moreover, the painted product, in turn, must be energized, but have a negative charge, in common people called "mass".
It is this technology that makes it difficult to color a metal product, but also to incorporate a coloring pigment into the molecular structure. If we talk about the advantages of this method of staining, then they will have to be listed for a very long time.
Therefore, we will focus only on the most significant ones that are directly related to the quality of coverage:
- High adhesion with any metal surfaces.
- Resistance even to significant temperature differences.
- Complete insensitivity to moisture and corrosion.
- Elasticity and resistance to mechanical damage. A product coated with a powder polymer does not lose a paint layer during deformation, which bends in the form of damage.
- The texture of powder paint is able to cover small flaws in the surface of the product.
- Powder paint is not only a decorative coating, but also with full additional protection of the product from all kinds of influences, both natural and mechanical.
Of course, this paint can not be called an ideal coating that does not have drawbacks, but they are all related to the technical side of the issue, that is, application and removal:
- If flaws were allowed during the staining process, then it will be very difficult to remove them later.
- As a rule, powder polymers are applied in three layers, which naturally affects the cost and speed of application.
- As mentioned above, for applying powder paint, you will need special equipment, which can not be dispensed with. Therefore, if you want to paint one product, then doing it yourself is unprofitable.
- Despite the fact that powder paint practically does not spread during application, the instructions for working with it provide for some experience and hardness of the hand.
- Only powder coating of metal products is possible, since other materials do not pass current, and therefore there will be no result.
As you can see, the ratio of positive and negative qualities of powder paint is almost the same, but, despite this, its popularity is growing from year to year.
Staining process
Despite the rather high cost, powder paints for metal have one interesting feature, namely, minimal losses during painting. This is relevant both for large factory workshops equipped with all necessary equipment, and for doing it yourself, when the paint is applied not in a special sealed chamber, but in a garage or other small room.
The secret is that in spite of the rather high pressure that the compressor gives out, the powder is blown out of the spray gun very slowly, and the painting takes place at a close distance from the metal, which prevents the paint from escaping in different directions. If we talk about specialized workshops, then powder coating of metal structures is carried out in sealed chambers, with special ventilation and a filter system.
Filters in this case perform two functions:
- Do not allow small particles of dust and flying debris to enter the camera.
- The particles of paint that have not come into contact with the product are captured and stored for future use.
Important! When staining in a self-made workshop, care must be taken to ensure complete sterility and tightness, since dust particles flying in the air can not only spoil the appearance of the product, but also disrupt the adhesion of the dye to the metal.
And you can clearly see the whole process of working with polymer powder dyes by watching the video in this article.
Polymerization
Another feature of powder dyes is that after application, they need polymerization, which takes place in another chamber under the influence of high temperatures.
Moreover, the temperature level directly depends on which dye layer polymerizes:
- Soil layer - polymerization at 160 degrees for 15 minutes.
- Paint coat - polymerization at 180-190 degrees, for 20 minutes.
- Superficial, decorative varnish coat - polymerization at 200 degrees for half an hour.
Heat treatment is necessary for powder dyes, as they melt and more densely set with the metal. Another plus of the polymerization process is that during the period of melting, the paint spreads throughout the product and penetrates into the places where the spray gun could not penetrate.
The camera itself is a sealed compartment, equipped with automation and thermocouples, which should be at least two. Since one measures the temperature at the bottom of the chamber, and the second at the top. Sensors and automation analyze both indicators and give an average level of heating.
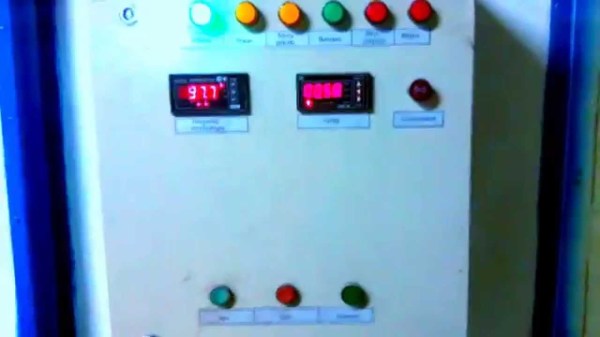
In addition, automation controls the temperature increase and keeps it at the required level for a given time.
By the way, the polymerization chamber can be built independently (see Do-it-yourself powder paint oven), for this it is necessary to have some knowledge of electrics in order to calculate and install heating elements. And also be able to handle the welding machine in order to build a frame.
Important! It is categorically not recommended to use one camera for painting and polymerization, since the paint deposited on the walls will come into contact with the metal and create insulation on the walls, as a result of which the temperature on the sensors will differ significantly from that which is actually in the camera.
The painted product is placed in the polymerization chamber after applying each layer and the required time is maintained, after which the heaters are turned off and the camera is allowed to cool to a temperature of about 100 degrees, after which the product is removed and the final cooling occurs already at room temperature. Then you can move on to the next layer of paint or decorative varnish.
To summarize
As you can see, the process of working with powder polymer paints is rather complicated and time-consuming, but taking into account all the positive characteristics of such a coating, you can compensate for most of the costs, since the painted product not only takes its original appearance, but also receives additional anti-corrosion protection, which they cannot boast no other types of paints.